In manufacturing, TIG welding, also known as Gas Tungsten Arc Welding (GTAW), is known for its precision and high-quality welds. TIG welding produces clean, precise welds with minimal spatter, making it ideal for applications requiring aesthetically pleasing welds of exceptional quality.
TIG welding is suitable, among other things, for:
- Stainless steels
- Aluminium and nickel alloys
- Particularly thin sheets of aluminium and stainless steel
- Special materials like titanium
TIG welding is a fusion welding process that uses the heat from an electric arc to create a weld joint. The non-melting, temperature-resistant tungsten electrode is an essential ingredient in this process. Welders can spend thousands of dollars on welding equipment, but unless due consideration is given to the selection and preparation the comparatively inexpensive electrodes, then their welding results can be poor, inconsistent, or simply fail.
What Determines Tungsten Performance?
Tungsten is one of the densest elements known, it has the highest melting point of all metals (3,410°C) and its characteristic hardness makes it very difficult to machine and forge in pure form. These properties make it an excellent choice for the production of TIG electrodes, but also make their manufacture a challenge. How these challenges are met has a significant impact on their quality.
Manufacturing Variables
The manufacture of tungsten electrodes involves a series of steps, each of which must be carried out with precision to obtain a quality, reproducible product. Because of tungsten’s very high melting point, it is not possible to simply melt the metal and cast the electrodes.
The manufacturing process follows these basic steps. Different manufacturers will use variations of these steps and sometimes, additional steps.
Tungsten powder production: This process first produces tungsten powder by reducing tungsten oxide (WO3) with hydrogen at high temperatures.
Addition of dopants: Other than pure tungsten electrodes, rare earth oxides are added to alter the physical and electrical properties of the electrode.
Pressing: The tungsten powder is pressed into the required shape and size.
Sintering: The pressed tungsten powder is then sintered in a controlled atmosphere to form a solid block. Sintering involves heating the pressed powder so that the individual particles bond together, forming a dense solid structure.
Machining: After sintering, the tungsten material is machined to achieve the final size, shape and finish required for the specific type of electrode.
Additional processes (optional): Depending on the specific requirements of the electrode, additional processes such as surface treatment, coating or precision grinding can be performed to further enhance the performance of the electrode.
Each of these steps affects the performance of the end product both initially, and over the life of the electrode.
Grain Size and Structure
Figure 1 shows the molecular structure of the inside of a point of tungsten and how it is divided into smaller groups called grains.
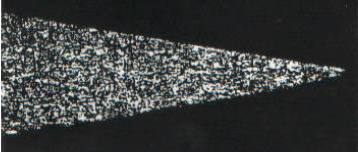
Oxides (the dopants) migrate to the tip primarily along the boundaries of these grains. It is much easier for the oxides to migrate along these boundaries than through the grains. Smaller grains provide more pathways for oxide migration but they also make it more difficult to obtain an even distribution of oxides. This balance is one of the challenges of manufacturing tungsten electrodes and also something that differentiates a quality electrode from a lesser electrode.
During welding, the grains tend to combine with larger neighbouring grains to form one large grain in a process called “grain growth.” However, if a continuous flow of oxides at the grain boundaries is maintained, this serves to surround the grains and keep them from combining. Thus, oxides are grain growth inhibitors. When tungsten runs out of oxides in any area, the grains combine readily, and the tungsten performs poorly because the oxides lack avenues to move to the surface.
Oxide Distribution and Size
Oxides should be distributed evenly throughout the tungsten. Uneven distribution results in poor performance: any areas with little or no oxides will tend to suffer from grain growth and areas with too much oxide will tend to “bottleneck”. For best performance, the oxide should be small to allow easy migration to the tip and be evenly distributed to ensure a constant flow.
Oxide (Dopant) Characteristics
Manufacturers have been doping tungsten since the beginning of the 20th century. Then, it was to improve the properties of electric light filaments. Much more recently, it is to improve the properties of tungsten electrodes for TIG and similar welding processes.
TIG electrodes can easily attain a cathode tip temperature near the melting point of tungsten. To reduce the electrode temperature and thereby, to increase the life of the electrodes, dopants such as Thoria (ThO2) and Lanthana (La2O3) are added to the tungsten. They generate a reduced work function by establishing a monolayer of emitter atoms on the tungsten tip.
The important properties of the dopant are discusses below.
Electron Work Function
The Work Function is the energy needed to remove an electron from the surface of a solid, and it is measured in electron volts (eV). The lower the work function of an electrode, the easier the arc starts. Oxides are added to a tungsten electrode to improve electron emission by lowering the work function of the tungsten.
Table 1 lists a selection of metals and their oxides and their respective work functions. The lower the eV for the oxide, the easier the arc will start. The metal work function is also important because, upon emitting an oxide, the metal is left as a film on the tip. The lower the eV of the metal at the tip, the lower the temperature will be at the tip. A lower tip temperature will:
- decrease grain growth,
- provide a constant flow of oxides and
- promote a longer service life.
Material |
Metal eV |
Oxide eV |
Lanthanum |
3.3 |
2.5 |
Thorium |
3.35 |
2.6 |
Thorium |
2.84 |
3.2 |
Pure Tungsten |
4.5 |
No oxide present |
Table 1: Physical Properties of Oxides
The more oxide that is added to the tungsten, the lower the work function that tungsten will have, and thus the better it will arc start. A 2% Lanthanated tungsten will arc start more easily than a 1% Lanthanated tungsten (assuming the same manufacturing process).
Note: electrodes from different manufacturers will behave differently because of differences in manufacturing procedures. A 2% Lanthanated tungsten from one manufacturer will be similar to, but not the same as, one from another manufacturer. If a change of electrode manufacturer is made, it is best to test the performance of the replacement electrodes.
Density
Each oxide has a different density. Thus a 2% by weight thorium, cerium, or lanthanum electrode will all have different amounts of oxides by volume. Table 5 describes the difference between density and weight for several materials.
Material | Density (g/cm3) | Volume % of 2% by weight electrode |
Lanthanum | 6.15 | 5.7 |
Thorium | 11.72 | 3.8 |
Cerium | 6.65 | 5.2 |
Table 5: Density versus Weight of an Oxide in a Material
Although each material has 2% by weight of the oxides, a 2% Lanthanated tungsten has a significantly higher volume of oxides than 2% Thoriated tungsten to feed to the tip.
Note: the amount of oxide present is specified by percentage weight.
Migration (Diffusion) and Evaporation Rates
The migration (also called diffusion) rate, is the rate at which each of the different oxides naturally travel from within the tungsten to the heat at the tip of the electrode.
The evaporation rate is the rate at which the oxides separate from their metal component and are emitted at the tip of the electrode. This is also called electrode wear.
The optimum-performing electrode is one that has a balance of good migration and evaporation rates. If the migration rate is slower than the evaporation rate, then there will be an inadequate supply of oxides arriving at the tip to maintain a consistent arc and the tungsten may be reduced to the performance level of pure tungsten. If the evaporation rate is slower than the migration rate, the oxides will be crowded at the point. If both of the rates are very high, welding properties at the beginning of welding will be good, but all of the oxides may be used up quickly.
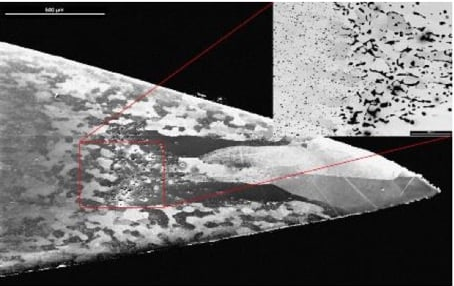
Multiple Dopants
In an effort to combine the advantages of several dopants in the one tungsten electrode, some manufacturers have used a blend of two, three or more rare-earth oxides. The objective is to optimise migration and evaporation rates, thereby prolonging the life of the tungsten while at the same time providing easy arc starts and a stable arc.
Electrode diameter and geometry
Electrode diameter (size) and geometry affect key attributes, such as current carrying capacity (and therefore electrode life), ease of arc starting, weld penetration and arc shape.
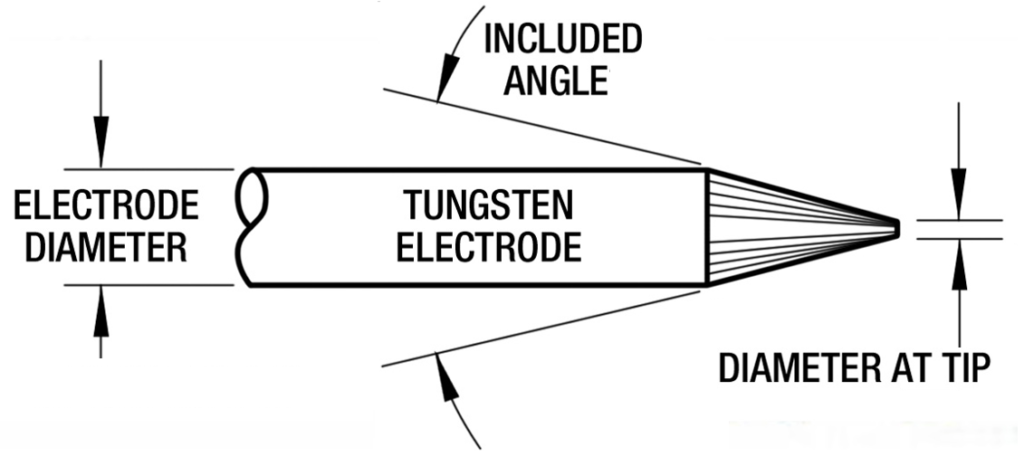
Electrode diameter (Size)
Electrode diameter primarily determines the current carrying capacity of the electrode. Manufacturer’s data should be consulted for the current range than can be used with the chosen electrode size.
A small electrode is easier to start but if it is too small for the current being used, it will overheat leading to potential splitting and melting of the tip. Any tungsten particles that subsequently fall into the weld will contaminate it.
A large electrode will handle more current and last longer, but may have difficulty arc starting and may have arc instability if the current is low.
Electrode geometry
The electrode geometry refers to the included angle (taper) of the tip of the electrode. The taper allows a compromise to be made between a larger electrode size and its higher current carrying capacity, and a smaller electrode that is easier to arc start and is more stable.
The taper should be ground longitudinally and concentrically using a dedicated diamond grinding wheel.
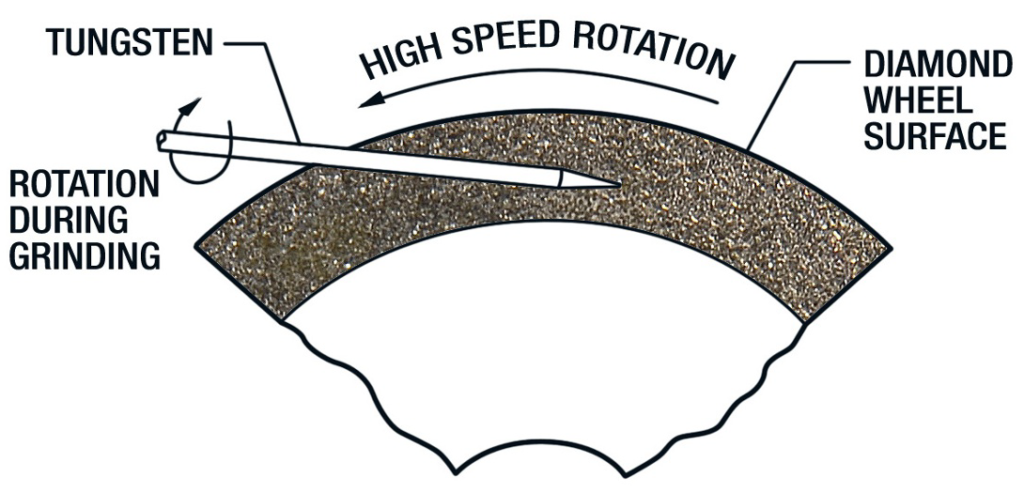


Electrons flow at a greater density on the surface of the electrode. If electrodes are ground or polished crosswise, the electrons have to jump across the grinding marks. The arc begins before the tip, spreads out and often wanders. The tungsten electrode becomes overheated and wears out more quickly. Longitudinal grinding allows an arc to start straight and remain stable and concentrated.
Different angles (like different sizes) produce different arc shapes and offer different weld penetration capabilities

SHARP TIP
- Improves the stability of the arc while welding with less amps
- Less weld penetration
- Shorter electrode life
- Wider weld bead
- Easier arc starting
BLUNT TIP
- Higher chance of the arc wandering while welding with more amps
- Better weld penetration
- Longer electrode life
- Narrower weld bead
- Harder arc starting
Blunt electrodes (large included angle) last longer, have better weld penetration, have a narrower arc shape and can handle more current without eroding.
Sharp electrodes (small included angle) erode faster, have a wider arc, have a more consistent arc and start more easily.
Electrode tip (flat)
The flat tip is another compromise, this time allowing the use of a small included angle but without having a sharp point that is likely to melt and contaminate the weld.
Manufacturers often list suggested flat sizes for their products and that is the best place to start.
Electrode Diameter /mm | Diameter At Tip /mm | Included Angle | DCEN Constant Current Range (A) | DCEN Pulsed Current Range (A) |
.040″ / 1.0 | .005″ / 0.125 | 12 | 2 to 15 | 2 to 25 |
.040″ / 1.0 | .010″ / 0.25 | 20 | 5 to 30 | 5 to 60 |
.060″ / 1.6 | .020″ / 0.5 | 25 | 8 to 50 | 8 to 100 |
.060″ / 1.6 | .030″ / 0.8 | 30 | 10 to 70 | 10 to 140 |
.093″ / 2.4 | .030″ / 0.8 | 35 | 12 to 90 | 12 to 180 |
.093″ / 2.4 | .045″ / 1.1 | 45 | 15 to 150 | 15 to 250 |
.125″ / 3.2 | .045″ / 1.1 | 60 | 20 to 200 | 20 to 300 |
.125″ / 3.2 | .060″ / 1.5 | 90 | 25 to 250 | 25 to 300 |
Tungsten Electrode Tip Shapes and Current Ranges for DCEN.
Current ranges for DCEP are about 10% of those listed for DCEN.
Current ranges for AC are about 50% of those listed for DCEN depending on the balance setting. The more cleaning, the less current can be carried.
Electrode preparation equipment
A dedicated tungsten electrode grinder is essential for creating the highest quality tungsten electrodes consistently. Standard bench-type grinders or Dremel modifications do not offer the ability to grind longitudinally or provide any guarantee of consistency from electrode to electrode. In addition, a non-dedicated grinder contaminates the electrode with foreign material that compromises weld quality in a number of ways.
While that is good advice for commercial welding organisations, a dedicated grinder can be quite expensive and out of reach for the casual welder. However, diamond electrode grinders/cutters that attach to a Dremel type tool are inexpensive and, with care, can give good results.
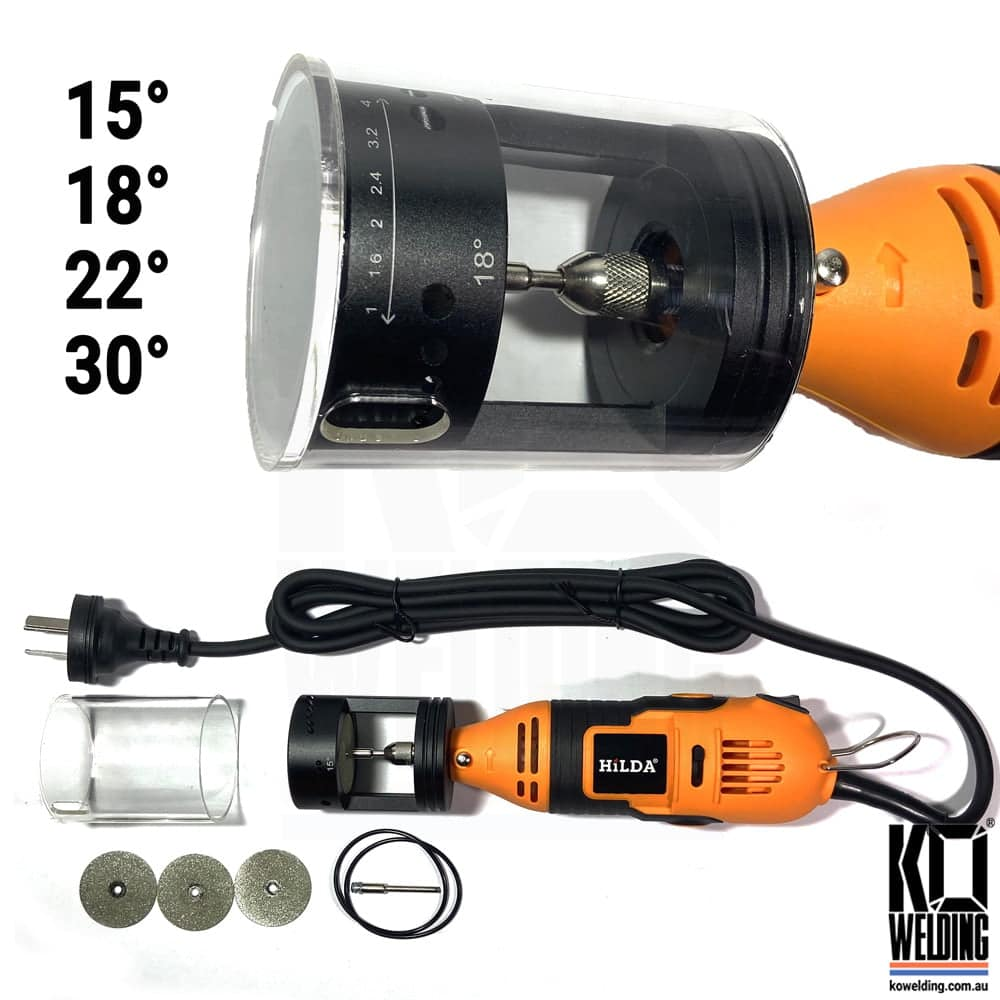
The important thing is to avoid the pedal driven sandstone grinder behind the shed and don’t use side cutters or a hammer to trim the length of an electrode.
Whatever method you use, keep the following in mind:
- Only grind longitudinally
- Use a diamond grinding wheel
- Aim for the smoothest finish possible
- Be consistent
- Dedicate the grinder to tungsten electrodes
- Don’t use tools like angle grinders, pliers and hammers when trimming the length of an electrode
Electrode Selection
This is where many look at any of the hundreds of WEB sites all over the Internet that list the features of each colour tungsten and how they work best for this material or that.
I have a different philosophy and a different approach. My philosophy is that tungstens are a work in progress and as discoveries are made, different dopants will be used in different amounts in search of the holy grail – a single tungsten for every application. Sometimes a combination of dopants will be used to take advantage of their individual properties.
A single tungsten for every application may be a dream but like much of science fiction, it eventually become science fact.
My approach is to select today’s best and then modify it to fit the task at hand. That means select the appropriate size electrode for the current being used, and then select a highly polished geometry to optimise arc starting, arc stability, penetration and susceptibility to weld contamination.
My choice is 2% Lanthanated (Blue) and I let the job at hand determine the electrode size and tip geometry. Your choice may be different but if you choose a modern doped or multi-doped tungsten, it’s not wrong, or worse, it is just different – maybe better.
Sources
In addition to learning from my own mistakes, I have used information (and some images) from a selection of tungsten electrode manufacturers and journals.
Manufacture and Doping of Tungsten Electrodes
- Luoyang forged tunsten-molybdenum material Co.,Ltd
- Abicor-Binzel – Alexander Binzel Schweisstechnik GmbH & Co. KG
- GCE – Gas Control Equipment
- DGP – Diamond Ground Products
Journals
- Journal of Applied Physics: Investigation of the flickering of La2O3 and ThO2 doped tungsten cathodes
- The Welder – thefabricator.com